GW LRUT – Guided Wave Long Range Ultrasonic testing
Long Range Ultrasonic testing (LRUT) also known as Guided Wave Ultrasonic testing (GWUT) is an Ultrasonic method wherein ultrasonic waves are transmitted along the pipe wall (guiding walls) up to 180meters in length.
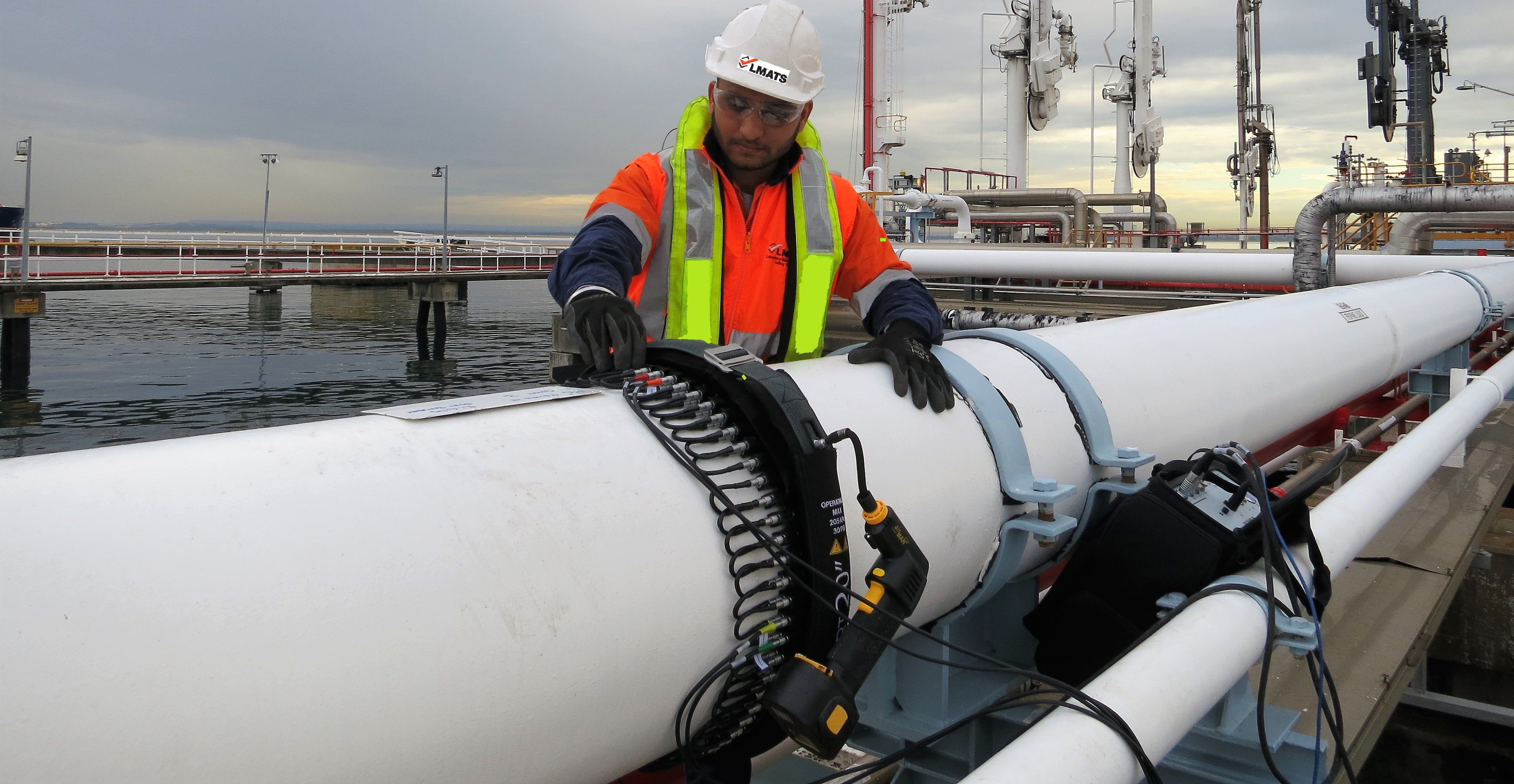
GW LRUT – Guided Wave Long Range Ultrasonic testing is a rapid screening test method for integrity assessment of pipelines, non-piggable buried, encased piping, vertical or inaccessible piping (e.g. overhead pipe racks) or epoxy coated pipelines to locate areas of potential degradation or engineering concerns and gross discontinuities for targeted assessment and inspection. While conventional NDT test methods provide localized inspection, underneath or in the vicinity of the sensors, LRUT is able to test 100% circumferential wall over tens of meters of the pipe length from the single inspection (contact point) location.
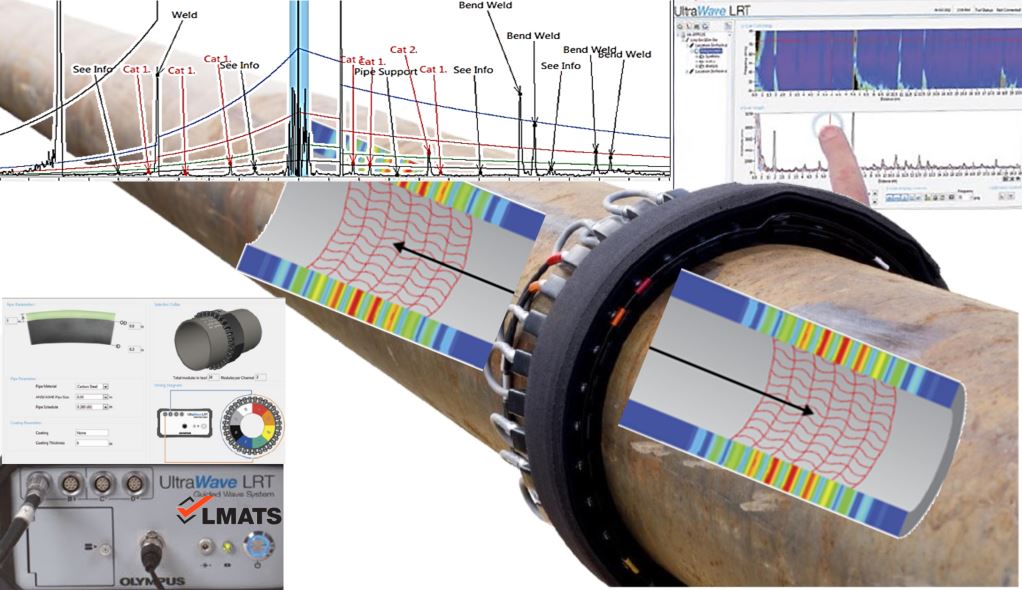
Guided Wave LRUT is used to inspect 100% of pipe circumference along the pipe length from a single location. Low frequency (15-85kHz) torsional or longitudinal guided waves are generated into the pipe body (360 degrees all around the pipe circumference) on both sides of the transducer assembly collar. These ultrasonic waves propagate in the axial direction of the pipe until the entire energy is attenuated or dissipated. When these guided waves intercepts areas of change in cross section such as butt welds, pipe supports, elbows, flanges or gross discontinuities such as severe corrosion, erosion, pitting clusters, etc; they reflect laminar waves back to the sensors at the location of wave initiation (Transducer assembly Collar). Multiple frequency signals are acquired simultaneously and analysed. The time-of-flight for each reflection and its dominant frequency is analysed to determine its location from the sensor. The quadrants determine the feature’s circumferential position on the pipe wall. The amplitude of the signal determines the significance of the defect in relative loss of cross section (LCS). The minimum LCS (loss of cross sectional area) that can be currently confidently detected is 3% of the total cross sectional area of the pipe under examination. One of the examples of representative cluster is shown in the following image.
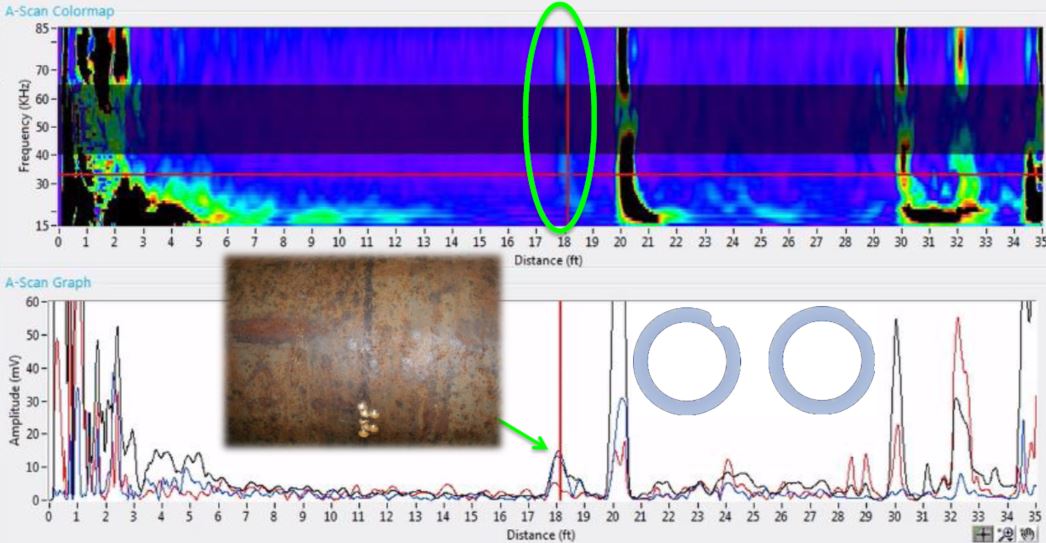
Guided Wave LRUT is primarily applied on pipelines having limited access or only localised access; to avoid unnecessary excavation, coating removal or scaffolding installation. The use of LRUT significantly reduces maintenance costs and is a perfect inspection method for unpiggable pipes or inaccessible pipe sections. LRUT can be used on pipe diameters ranging from 38mm (1.5”) to 1200mm (48”) to detect loss of cross section (LSC) or areas of concern such as corrosion or erosion pockets around the pipe's circumference. The sensitivity of the LRUT is typically 2.5% LSC, equally sensitive on both ID and OD of the pipe. Absolute defect size will depend on the pipe size (for large ODs and wall thickness, 5% can be a penetrating defect). The signal amplitude will depend on the shape of a discontinuity e.g. extended area over the circumference or the extended depth in the wall. LRUT can be performed on in-service pipelines operating in the range of 0°C to 70°C. Testing can be done at higher temperatures and as low as -30°C but with exceptional risk management plans. Moreover, LRUT can be applied on various materials and different pipe diameters having wall thickness up to 40mm.
ASTM E2775 outlines a procedure for using GWUT on tubular carbon steel or low-alloy steel products having Nominal Pipe size (NPS) 2" to 48", and for wall thickness between 3.8 and 25.4 mm.
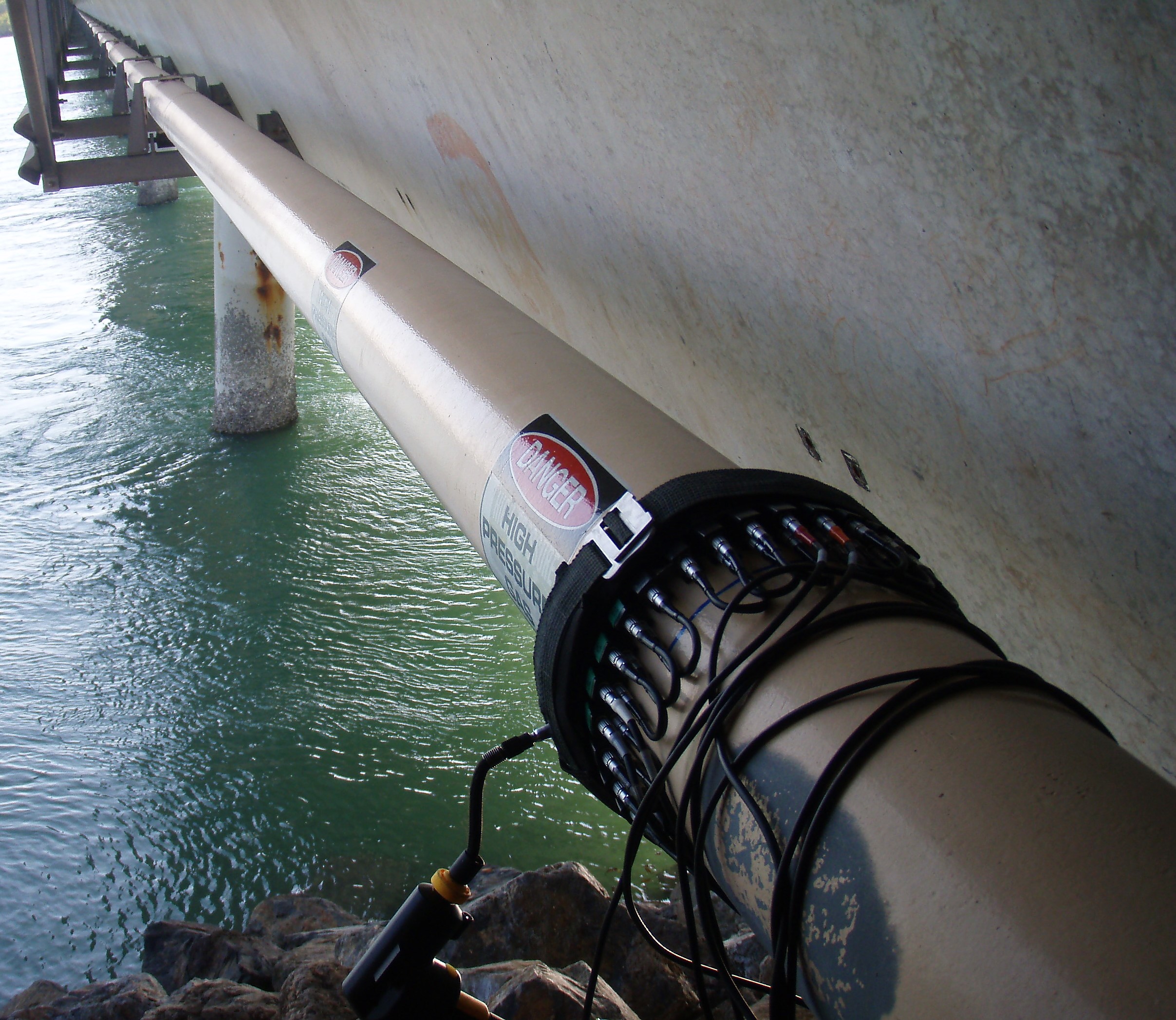
Typical scanning (interpretable) range from the single test location is the maximum ± 90 meters in each direction (180meters bidirectionally) for above ground or encased pipelines. The interpretation distance from the single location can be reduced by the following parameters.
- Pipeline layout such as several bends, attachments, supports, branches & joints
- Highly viscous liquid deposits on the internal or external pipewall.
- Entire pipeline is severely corroded (Rapid attenuation of ultrasound and excessive noise reduces interpretable lengths of pipeline)
- The type of coating e.g. Bitumin is a viscous liquid which dampens ultrasound.
- Excessive thickness, diameter and the material of the pipeline
Generally, inspection range is set in relation to the defect size sought (sensitivity) and the attenuation of sound.
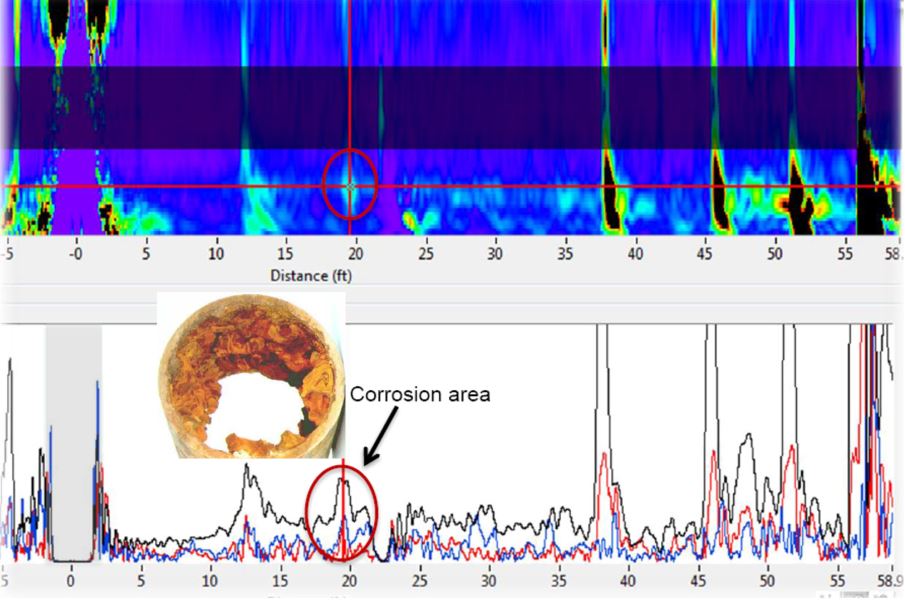
Ideal Applications:
Guided Wave Long Range Ultrasonic testing (GW LRUT) can be used for
- Rapid inspection of in-service pipelines and piping for detecting corrosion or areas of concern (LCS)
- Buried pipelines at the excavation locations or at level crossings
- Encased (through-wall) pipelines or culvert line or PE coated pipes
- Vertical pipes or structural circular columns
- Inaccessible piping e.g. overhead piping rack
- Requirement for high speed assessment to reduce cost reduction - Eliminate the cost of complete scaffolding or use of Elevated working platforms due to which testing speed is reduced.
- Insulated pipelines and piping – No need to remove entire pipeline insulation
- Detection of corrosion at pipe supports, clamps and pipe racks
- Refinery, chemical plants, power station piping
- Risers and offshore topside pipe work
- Jetty lines and river crossing pipelines, tank farm link lines and sewer lines
- Detection of Weld Root Erosion (See following image)
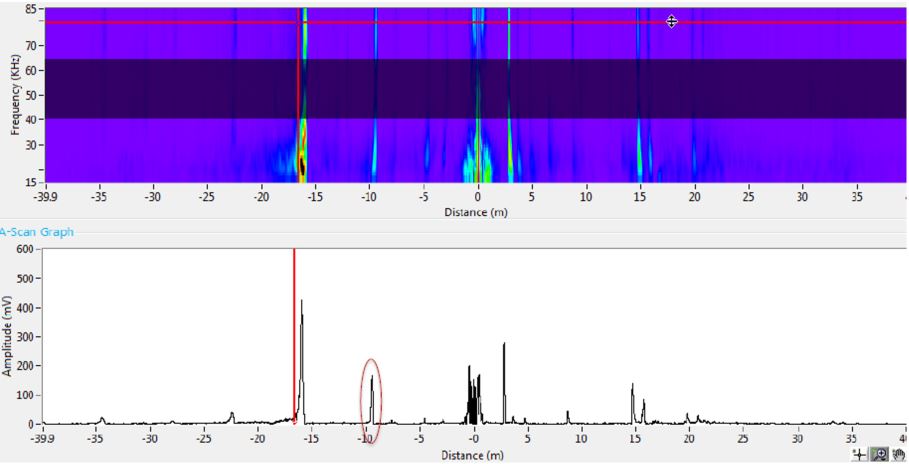
Advantages:
- In-service inspection prevents production losses or downtime.
- High productivity inspection - Reduction in onsite inspection time – maximum examination speed is 180meters per hour.
- Examine 180meters (90m from each side of the transducers) from the single test location
- Examine 100% of the pipe circumferential wall from the single test location (contact point)
- Maintenance cost reduction by not removing
- surface coating of the entire pipeline except 500mm width exposed to attach transducers.
- insulation of the entire pipeline, except 500mm exposed to attach transducers.
- No need to sand blast or grind entire pipeline surface under examination
- No need to excavate the entire non-piggable pipeline or random spot tests
- No need for a couplant which is necessary in conventional ultrasonics.
- Detects weld root erosion faster than conventional test methods
- Detects corrosion (loss of cross section) at pipe support. See image below
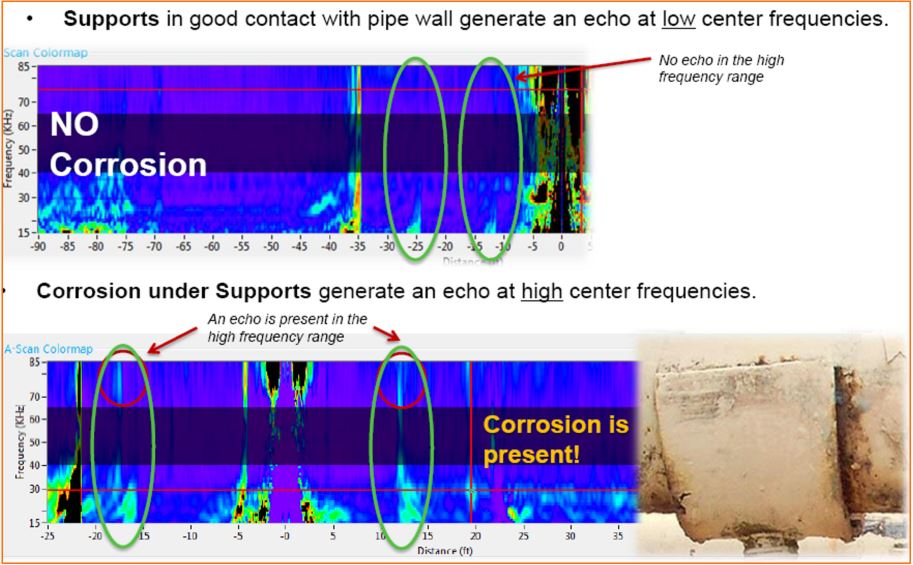
-
Limitations:
- Guided Wave LRUT is a screening test method and hence precise measurement of minimum wall thickness (like PAUT) is not possible. After an area of concern is detected, average wall thickness measurements can be completed by Pulsed Eddy Current testing (PECT) as a faster technology. For precise wall thickness measurements, Phased Array Ultrasonic testing (PAUT) is recommended. For localised wall thickness measurement, conventional compression (longitudinal) wave ultrasonic testing can be applied.
- Cannot detect an Isolated pit.
- Testing of Cryogenic pipelines is possible but difficult – Exposed test location will condensate heavily and also the transducer may not detach from the frozen pipe wall surface.
- Bitumin coated pipelines or buried pipes in contact with wet soil and wet silt or severely pitted pipelines attenuate sound severely and hence they are difficult to inspect.
- 100% surface area around the fillet weld cannot be assessed due to joint configurations.
- Pipes less than 1.5inch diameter are currently not feasible to examine.
- Minimum pipe length shall be 5meters for cost effective LRUT application.
Typical test range possible on different pipelines:
Pipeline type / condition |
Probable Test range (in each direction) |
Typical |
Minimum length |
Maximum length |
Attenuation |
Clean straight pipe |
50 |
200 |
-0.15 to -0.5dB/m |
Kevlar wrapped |
30 |
200 |
-0.15 to -1dB/m |
Clean, wool insulated |
40 |
175 |
-0.5 to -1.5dB/m |
Insignificant minor corrosion |
20 |
50 |
-0.5 to -1.5dB/m |
Spun epoxy coating |
30 |
50 |
-0.75 to -1dB/m |
Significant corrosion |
15 |
30 |
-1 to -2dB/m |
Well packed earth |
15 |
30 |
-1 to -2dB/m |
Grout lined pipe |
10 |
30 |
-1 to -3dB/m |
Bitumen tape - thin (<2.5mm) hard |
5 |
25 |
-1.25 to -6dB/m |
Bitumen tape - thick (>2.5mm) soft |
2 |
8 |
-4 to -16dB/m |
Concrete wall - loosely bonded |
2 |
8 |
-4 to -16dB/m |
Concrete wall - well bonded |
1 |
2 |
-16 to -32dB/m |
Steel Pylons / Piles or pipeline under water = Approximately 15m minimum
Buried pipeline - dense clay embedded, Coal tar enamel coated in Victoria = 10m on each side of the Transducers
Expertise:
LMATS utilizes the latest technology LRUT instrument from Olympus, the UltraWave system. The UltraWave LRUT system is a higher resolution instrument as compared to some other technologies. One of the feature is having 1 kHz adjustable steps within a frequency spectrum of 15 to 85 kHz to evaluate signals better. As the GWUT is frequency dependent analysis, the software for this latest technology LRUT system is equipped with a unique F-scan color map that displays the entire frequency range acquired over the inspected pipe length. Olympus LRUT system also includes the active focusing capability to reduce signal-to-noise ratio which enhances flaw evaluation by delivering concentrated energy at a specific location on the pipe. The energy can be focused at eight different positions around the circumference, investigating the pipe cross-section, segment by segment. This active focusing estimates the circumferential extent of the indication by displaying a Polar graph.
LMATS LRUT system is a portable back-pack carry on system (8kg), battery operated which can performed by a single person.
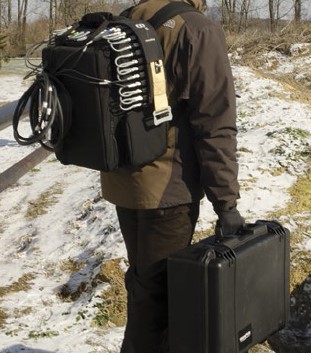
Compared to conventional ultrasonic testing, Guided Wave LRUT instrument, transducers and software are complex and thus expensive. This test method requires highly trained, skilled and experienced personnel. LMATS has trained, certified and experienced engineers to provide Guided Wave Long Range Ultrasonic testing (GW LRUT).
LMATS offers Guided Wave Long Range Ultrasonic testing (GW LRUT) testing from our Melbourne, Sydney, Brisbane, Perth and Albury laboratories. LMATS regularly performs Guided Wave Long Range Ultrasonic testing (GW LRUT) testing in VIC -Victoria, NSW - New South Wales, QLD - Queensland, WA - Western Australian, SA - South Australia, TAS - Tasmania, NT -Northern Territory and some of the neighbouring countries at request.
To find out more about LMATS Guided Wave Long Range Ultrasonic testing (GW LRUT) Advanced NDT Capability, simply contact one of our laboratories nearest to your location or call on + 9399 8145 or via the form
Frequently asked Questions:
FAQ1 – What is the level of surface preparation required at the LRUT contact point?
Advice – If the coating system is of good quality and adequately adhered to the pipe surface then no additional need for surface preparation. But in most cases, the coating condition is of unacceptable quality or coating flaking off. Hence it is recommended to sand blast or remove surface coating of 500mm width around the pipe circumference. This location should be preferentially chosen away from a butt weld or a flange end.
FAQ2 – Can LMATS perform LRUT on my cast iron pipeline?
Advice – Yes, LMATS can perform LRUT on your cast iron pipeline, conditional to that the pipes are metallurgically bonded (e.g welded) and not joined by flanges or screw joints. If later is the case, then each pipe will need to be scanned individually using LRUT single point of contact system.
Graphitization is the common mode of corrosion in cast iron pipes. LRUT should be able to detect considerable graphitization (non-conductive layer) when the sound conductive loss of cross section has occurred. The sensitivity may not be as effective as it will be on carbon steel pipes.
Note – Most of the cast iron pipes are either bell type joint (with rubber inserts) making them conductivity wise non-continuous pipeline. Hence each of the pipes will require LRUT assessment. LRUT has a near zone effect of 1m. This means a typical 2.4m pipe will need scanning from both ends of the pipe.
Alternative for this is to use Magnetostrictive collars which produces slightly higher frequencies and has shorter near filed zone. This test method is like Short range guided wave ultrasonic.
If LRUT or SRUT is not a possibility for your pipe then MFL is recommended.
LRUT does not require couplant as is the case in conventional ultrasonic. But in-service cast iron pipe may have textured surface which may not permit LRUT dry coupling.
FAQ3 – What types of materials can be inspected by LRUT?
Advice – Carbon steel, alloy steel, stainless steel, Cast iron, etc
FAQ4 – Can LMATS perform LRUT on the in-service pipeline (piping) and assess the quality of welds?
Advice – Although, LRUT cannot assess 100% of the weld quality, the test system can detect lack of penetration, excessive penetration, weld root erosion or severe corrosion in the HAZ.
FAQ5 – Can LMATS perform LRUT near a fillet weld or a number of bends on pipelines?
Advice – Yes, LMATS can perform assessment near a fillet weld using a LRUT by placing the transducer assembly away from the fillet weld. LMATS will need to evaluate the other side of the fillet weld (or Tee branch) by placing the LRUT collar again on the other side of the fillet on the pipeline.
Similarly, the first or second bend can be examined from one side of the pipeline and then assessing from the other side of the bend.
FAQ6 – How many bends can be covered in the single scan by your LRUT system?
Advice – LMATS experienced engineers will be able to interpret data for up to 2 bends or 2 branches, depending on the attenuation of ultrasound due to your pipeline condition and signal to noise ratio. It may be required to collect data at additional locations to cover 100% of the bend zone.
FAQ7 – I have a pipe rack system that needs 100% inspection but there is limited space between pipes to conduct NDT. What type of NDT can be applied?
Advice – LMATS LRUT collar is only 30mm thick. If temporary space can be created between pipes at the collar mounting location (for the period of maximum 30 minutes), then LMATS experienced engineers will be able to attach transducers collar and perform testing for tens of meters of pipe length.
FAQ8 – I have read that the LRUT is not possible near the flange end. Can your system test near the flange end?
Advice – When the LRUT collar is placed near the flange end, a lot of energy is reflected towards the transducers, making it difficult for the trained personnel to differentiate signals. The flange end of the pipe can be examined by attaching the transducer assembly further away from the flange end and transmit ultrasound towards the flange end. There is no need to place the LRUT collar at the flange end to assess this area. In unavoidable circumstances, wherein there is very limited access, and for the best signal quality, LMATS experienced engineers will position the collar in such a manner that the first ring of transducers is approximately 60mm from the start of the flange.
FAQ8 – Can LMATS LRUT detect corrosion in my severely corroded pipeline?
Advice – LRUT is a test method to find abnormality (discontinuities) in a deemed to be normal pipeline. If the pipeline is already severely corroded then LRUT is not a suitable solution. But if the asset owner assumes that the pipeline under test is normal then LRUT can diagnose that the pipeline is severely corroded by interpreting the LRUT signals.
FAQ9 – Can Guided wave LRUT be applied on a spiral welded steel pile?
Advice – Yes, LRUT can be performed on Jetty piles. LMATS has performed LRUT on Jetty piles (48”, 16mm wall thickness). Barnacles and other similar things around the steel wall attenuates ultrasound rapidly. Our experience indicates that the interpretable data can be obtained for 8 to 10m length of pipe immersed in the water. Small diameter steel piles may provide interpretable data for longer lengths of the pipe in the water path.